CLEAN ENERGY AT THE SERVICE OF ECOLOGY
Continuus Properzi is dedicated to minimizing the environmental footprint of both its operations and those of its end users. The company diligently monitors greenhouse gas emissions, advocates for energy efficiency, and embraces sustainable practices in the stewardship of natural resources. Actively investing in eco-friendly technologies, Continuus Properzi also encourages the adoption of sustainable practices within its supplier and business partner network. By promoting responsible innovation through ongoing research and development of sustainable solutions, the company strives to proactively address and respond to global challenges. Through these efforts, Continuus Properzi aims to contribute to a more sustainable future for generations to come.
REDUCTION OF THE CARBON FOOTPRINT
Solidification
During Solidification of the liquid aluminium into Ingots and in the following phase to remelt the Al ingots for the production of the downstream products:
- A detailed study of all the savings, including other benefits of our ingot casting technology, the elimination of ‘out-of-dimension’ ingots and transportation of the same, has provided evidence that “CO2ntinuus Green Ingots” emissions of CO2, are greatly reduced. Moreover, our ingots if compared to traditional ingots solidified in an open top mould and with other ingot types available on the market, are Greener with a savings of 280 kg CO2 -eq per ton of primary Al ingots.
- Moreover, our ingots if compared to traditional ingots solidified in an open top mould and with other ingot types available on the market, are Greener with a savings of 280 kg CO2 -eq per ton of primary Al ingots.
Refining
In Refining technology for the production of CU Green wire, and more specifically from refining from scrap:
- The production of FRHC (Fire Refined High Conductivity) Cu products from secondary Cu, that can replace with almost identical characteristics Cu products starting from primary Cu, thanks to the Properzi refining technology can reduce the Carbon Footprint by as much as 7’000 Kg CO2-eq per ton of FRHC copper rod products, processing 100% copper scrap (old and/or new).
SELF ANNEALING MICROROLLING®
With our Self Annealing Microrolling® technology that facilitates a 50% energy savings:
- Cu Green Wire: savings up to 50% of electrical energy per ton of 1.8-2.6mm wire starting from 8mm rod.
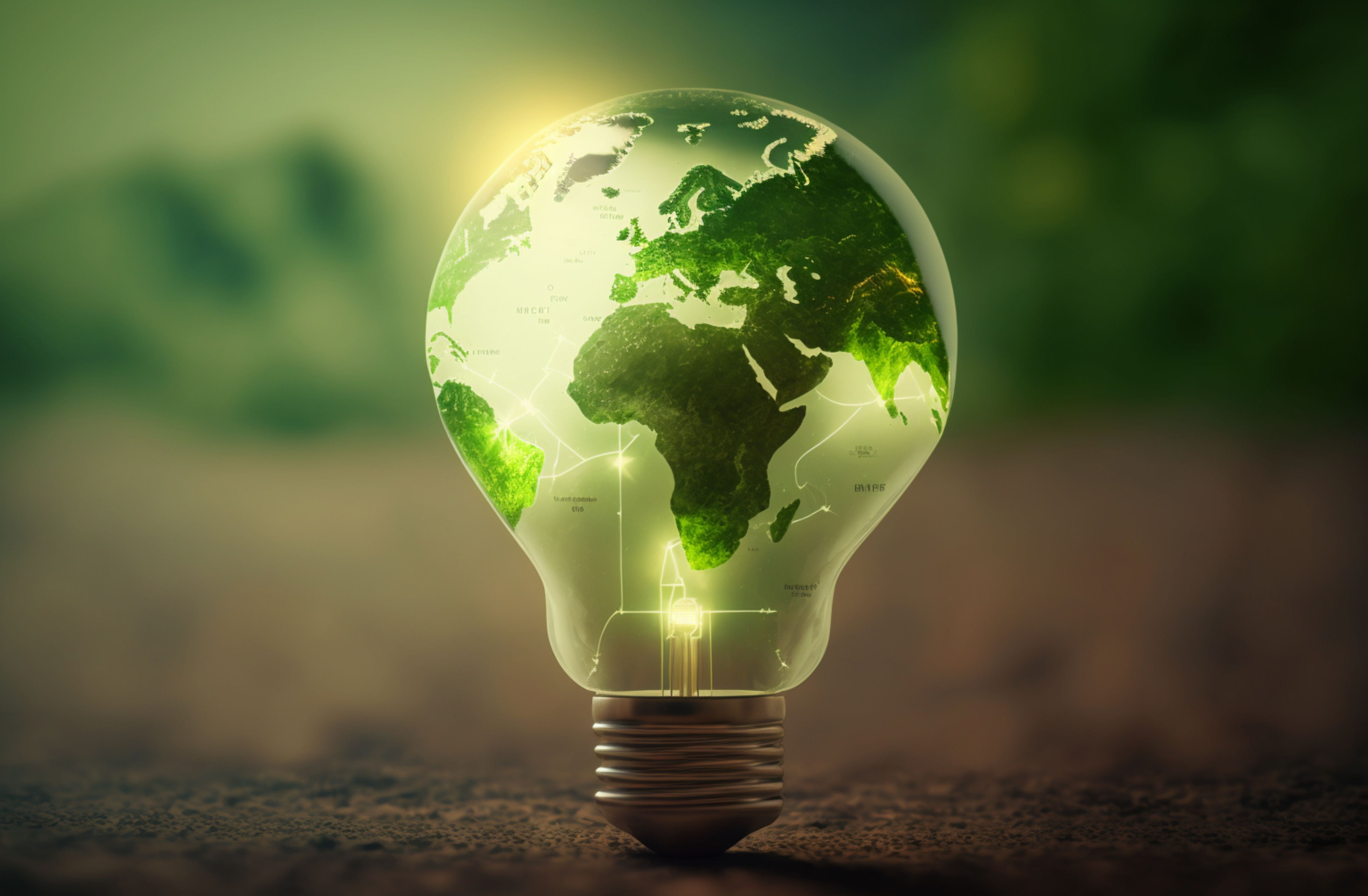
Energy efficiency
Aluminium field
In the AL field our Vert-Melt (Vertical Melting) Furnace offers several advantages including: much higher energy efficiency compared to any type of reverberatory furnace (1 to 1.5 % versus 3 to 5 %), lower emissions, and 25% less gas consumption. Furthermore, allows the saving of 420 Kg CO2-eq per ton of Al ingots melted and compared with the traditional melting furnaces; it is an example of green technology not only for energy efficiency, but also for dross generated and significant reduced emissions.
Copper field
In the CU filed let’s turn our attention to “recycling” and therefore on the production of copper wire rod starting from scrap. Recycling of copper scrap is also one of the best examples of a circular economy. Melting, refining and casting the desired final product according to Properzi know-how, accumulated during 30+ years of experience, allows great economic savings and avoids additional exploitation of the mines. Properzi’s scrap recycling technology fits perfectly into this context, allowing greater energy efficiency as the production phases are significantly reduced.
Refining furnaces
The Refining Furnace with a capacity of 250 tons per day is a Properzi scrap refining furnace for the production of copper wire rod. With the new geometrical configuration of the furnaces, by placing a large door in an elevated position served by an inexpensive skip charging machine, we are able to achieve significantly improved thermal efficiency due to the enormous quantity of Cu scrap loaded through the charging door (patented by Giulio Properzi, inventor of several new solutions serving the non-ferrous industry). When the charging door is on top of the furnace body, the scrap can be conveyed through a smaller door thereby minimizing the escape of heat and pollutant fumes!
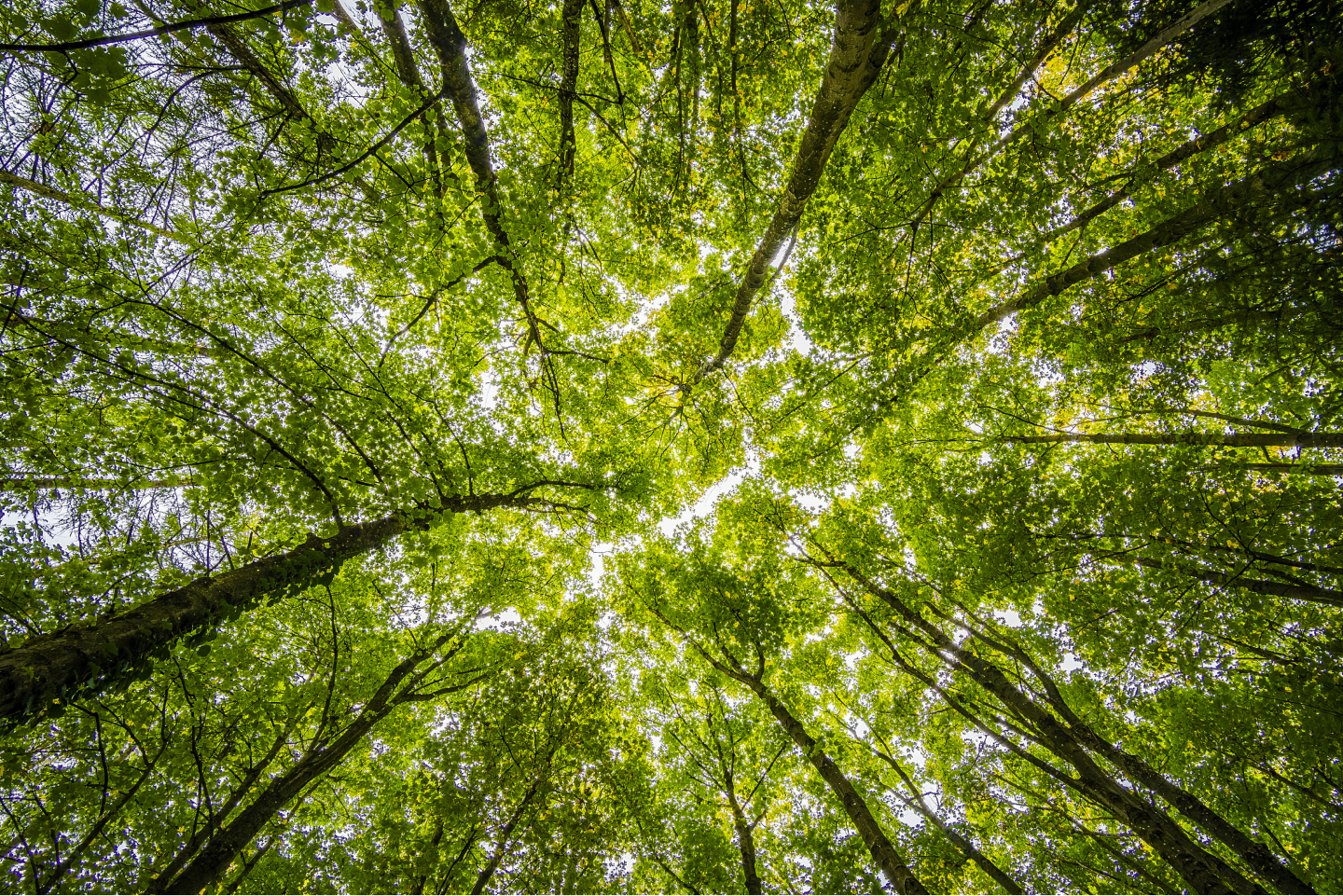
Green vision & reality
Today, our company is investing significant capital in the purchase of state-of-the-art machine tools, which make use of energy recovery systems and optimally sized refrigeration systems. The combination of these factors with energy-saving control techniques, such as evening deactivation and minimization of the heating phase, ensure reduced energy requirements and integrated efficiency.
If you have a chance to visit us at our headquarters, we are sure you will immediately understand Continuus-Properzi’s commitment to being not only an inventor of new technologies that has changed traditional industrial practices in the nonferrous industry, but also our strong commitment to the environment and sustainability that is an integral part of our company. This is evident in our headquarters, with 20,000 square meters of greenery and hundreds of trees that existed when the company moved to its current location; now these same trees are more than 75 years old.