Copper
Copper ETP Rod Lines
The demand for Electrolytic Tough Pitch (ETP) copper rod is growing at a rate of 3.5 – 4.0% y-o-y and Properzi can say that the technical requirements for copper rod are becoming more and more severe year after year.
Anticipating the market needs, Continuus-Properzi has evolved into a real EPC (Engineering, Procurement and Construction) supplier with the most worldwide experience and relevant know-how regarding complete Electrolytic Tough Pitch (ETP) wire rod lines, from furnaces to coiler, for the copper rod and wire industry.
Standard plants available in OUR production program
Small
- from 5.0 tph to 10.0 tph
- expected yearly output: from 25,000 t to 58,000 t
Medium
- from 12.5 tph to 20.0 tph
- expected yearly output: from 61,000 t to 115,000 t
Large
- from 25.0 tph to 50.0 tph
- expected yearly output: 125,000 t to 310,000 t
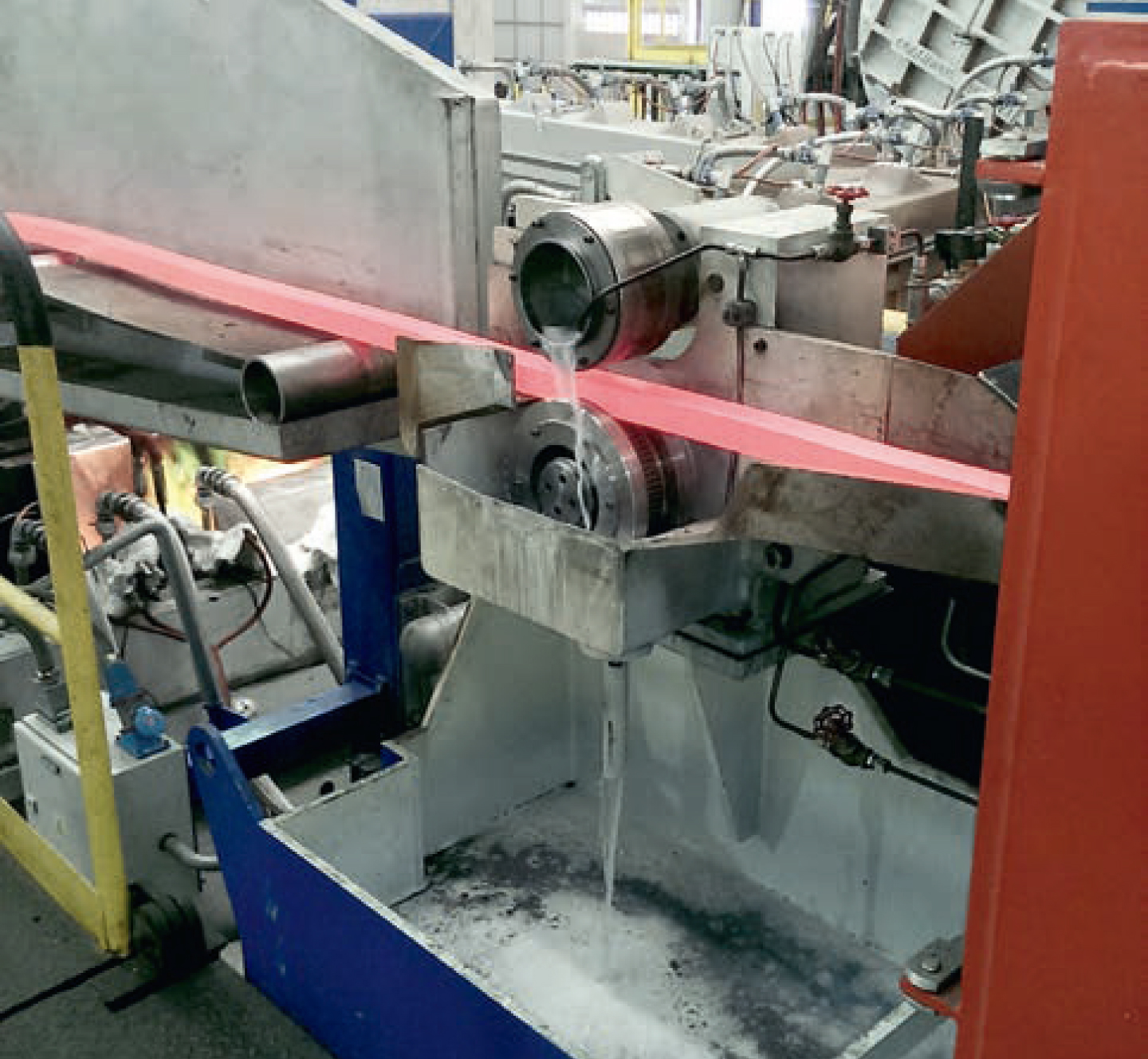
MAIN ADVANTAGES
Highest worldwide percentage of premium quality | Widest range of commercial Cu Rod diameters | Best geometrical quality |
Maximum flexibility in processing Cu cathodes, even of low quality | Perfect coil shape in both concentric and orbital types | Rod quality repeatable and constant |
Highest rod quality for ETP, exceeding the standards | Increased mechanical properties |
CCR COPPER typical lines configuration
Close –
View +
Close –
View +
*The CCR Line provides a typical line configuration. The position of the main equipment can vary according to specific needs:
00. FUME TREATMENTS |
01. REFINING FURNACE (SET) |
02. SHAFT FURNACE AND HOLDING FURNACE |
03. CASTING MACHINE |
04. AUTOMATIC BAR SHEAR |
05. BAR PREPARATION UNIT |
06. ROLLING MILL |
07. PICKLING UNIT |
08. COOLING UNIT |
09. WAXING UNIT |
10. COILER |
11. CONTROL ROOM & ELECTRICAL CONTROL CABINETS |