From rod to wire
MICROROLLING®
The Microrolling® Mill’s main objective was to become an advantageous alternative to the conventional breakdown machines (cold drawing). The Properzi Microrolling® technology was first brought to market in 1979 and has been very well proven for processing wire rod in both hot and cold rolling conditions.
Innovations for Aluminium/Copper Industries
Our latest innovations for the Properzi Microrolling® technology cater to both the aluminium and copper industries.
• Our Microrolling® technology is used for both a hot rolling process and a cold rolling process within the production of aluminium welding wire. The hot process is a continuous cast wire (CCW) line where molten aluminium (specifically welding alloys) is continuously cast and rolled via an eight-stand Microrolling® mill (hot rolling process) to produce 6 mm wire. The subsequent cold process, which replaces a traditional breakdown drawing machine, is a second eight-stand Microrolling® mill, almost identical to the rolling mill used in the CCW line, that further processes the 6 mm material to a diameter of 2.15 mm. This integrated process is flexible, appropriately sized, energy efficient, and easily controllable from molten metal to the final product.
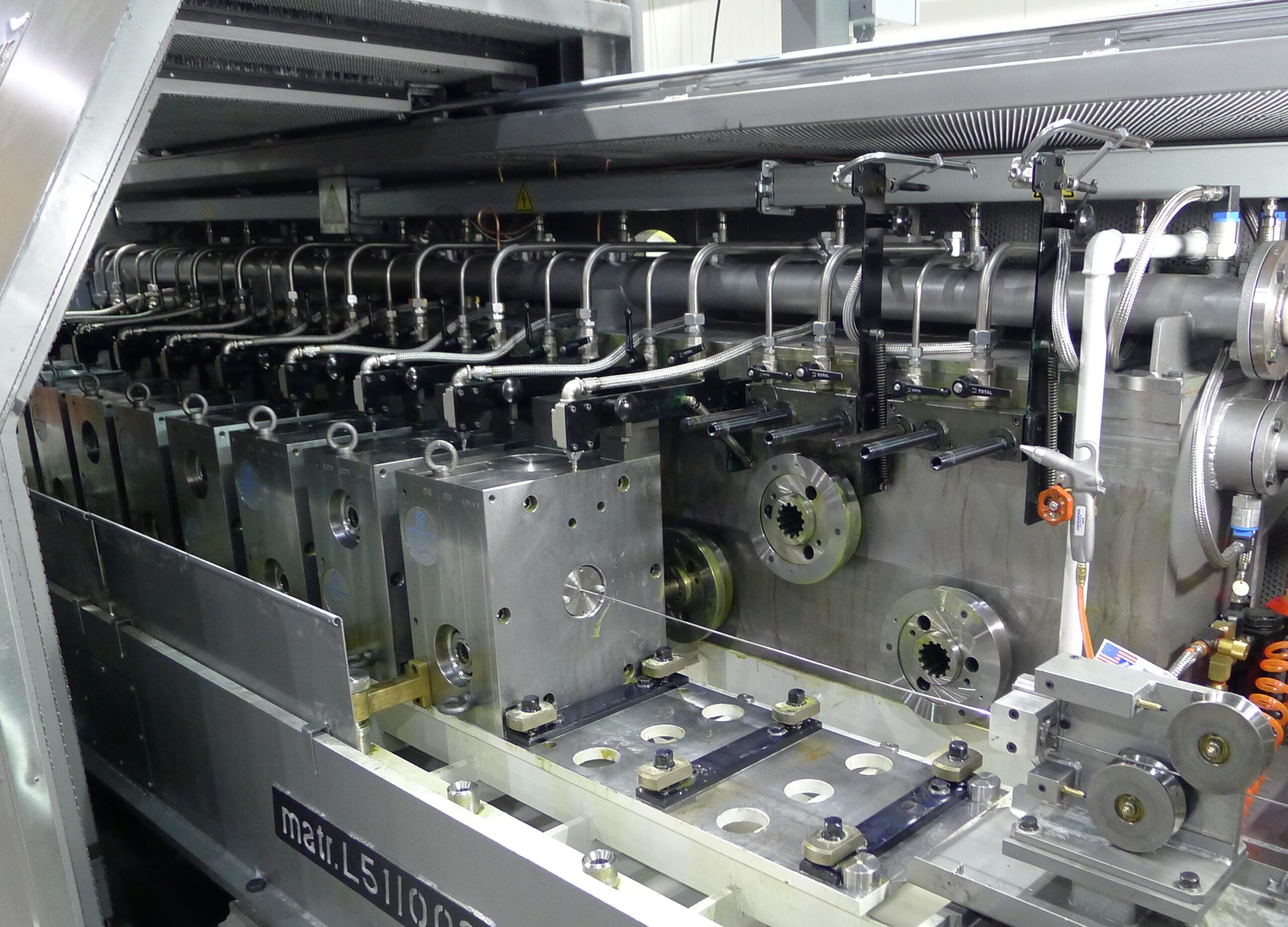
MAIN ADVANTAGES OF THE MICROROLLING® MILL COMPARED TO A TRADITIONAL BREAKDOWN DRAWING MACHINE
Energy savings | Low maintenance | Self-threading (extremely user-friendly) |
Increased safety (self-threading eliminates potential pinch points) | No pointing required and no rod pickling required | All together: lower production costs |
Reduced work hardening of the material | Improved wire surface smoothness | Absence of residual lubricant on wire surface |
Possibility of hot rolling without loss in output and efficiency | Greater reduction between anneals on hard material | Possibility to eliminate intermediate anneals |
From rod to wire
SELF-ANNEALING MICROROLLING® – SAM
Our company has applied a further set to this technology: The patented Properzi Self-Annealing Microrolling® (SAM) method uses the Properzi Microrolling® technology and replaces the conventional drawing/annealing processes while providing tremendous energy savings.
Giulio Properzi’s patented idea is based on the Properzi Microrolling® process and a fundamental concept of physics: the Law of Conservation of Energy that states energy can neither be created nor destroyed but can be changed from one form to another.
- It is a sophisticated machine consuming 80-90 kWh/t per ton only getting the desired elongation of the wire – usually around 30% – for the subsequent drawing process in Multi-wire Machines.
- While in Drawing Machine the wire must remain at low temperature, a rolling mill can work at high temperature
- The rolling power, is totally transformed in heating energy and a part of it can increase the temperature of the wire during the rolling process to levels above the annealing temperature.
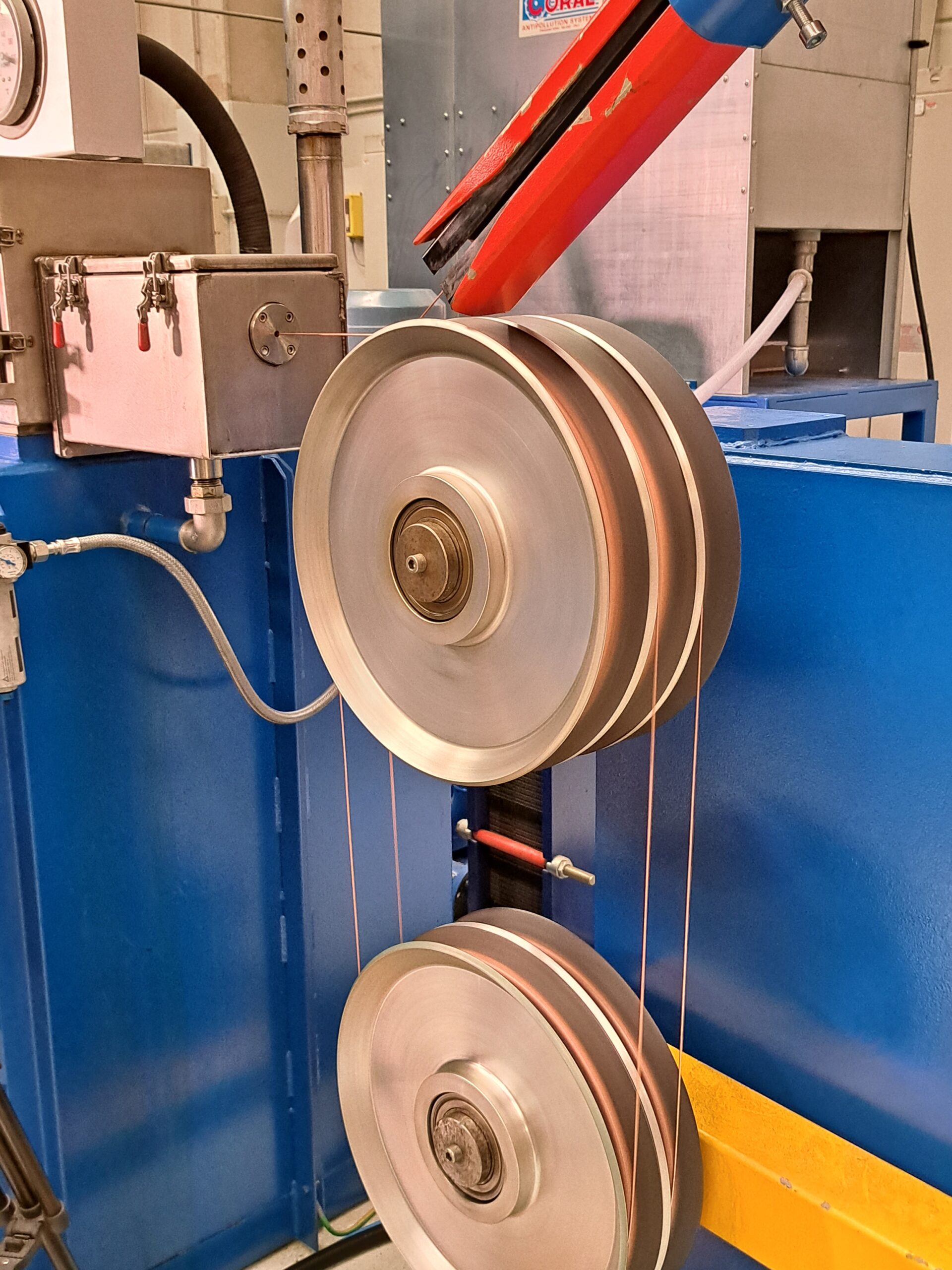
MAIN ADVANTAGES
No annealer required | Less than € 100.000 per year in energy cost | Compact lay-out |
Up to 100 kWh/t saved (not only is annealing energy saved but also the deformation power required is less because the copper is rolled at an elevated temperature) | Zero energy for annealing | No maintenance required |
Properzi equipment installed since our founding in 1947.
*It may not coincide with the number of Properzi plants currently in operation.